protecting nature
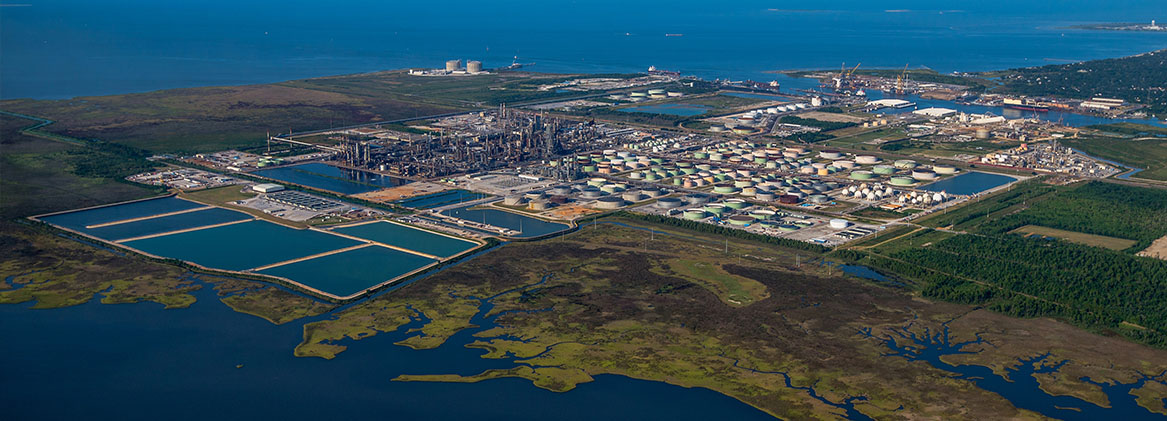
reducing environmental impact to air, water and land
Chevron’s Pascagoula (Refinery) is committed to protecting the environment and community by employing effective measures to monitor, manage, and reduce emissions from our operations. The Refinery uses various types of control technologies to minimize the facility’s environmental footprint. We monitor and analyze emissions control equipment to ensure plants are operating within regulatory air quality standards and permitted limits.
Nitrogen oxides (NOx) and Sulfur dioxide (SO2) emissions at the Refinery have decreased by approximately 70 percent since 2005. This has been achieved as part of an ongoing effort which includes:
• installation of a state-of-the-art Flare Gas Recovery system
• additional tail gas units for Sulfur Recovery plants
• installation of pollution controls on existing furnaces
• replacing outdated steam boilers with new equipment with better emissions controls
The Refinery continues to seek opportunities to reduce Volatile Organic Compounds (VOCs) emissions. The Refinery manages several inspection, leak detection, and repair programs for various types of equipment such as valves, pumps, cooling towers, and tanks. Vapor recovery systems are used to control VOC emissions from loading operations at the wharf and marketing terminal. Lastly, emissions from chemicals are reduced by using, devices such as carbon absorption canisters. These canisters control substances such as benzene and hydrogen sulfide.
A flare is a safety device used to eliminate excess pressure buildup in certain equipment and processes in the Refinery. Whenever pressure in the plant begins to rise, the material is safely diverted to a relief system equipped with a flare gas recovery system. This system captures the diverted material, and it is reused within the refinery. Any material that cannot be recovered is combusted in highly efficient flares.
Occasionally, you may see smoke coming from the flares. This may happen during events when material cannot be recovered by the flare gas recovery system. We strive to avoid and mitigate such unplanned events.
The refinery continues to employ new technology and procedures that reduce waste generation or recover waste and transform it into useful products. We reduce waste by decreasing waste sources, recycling, using less hazardous materials, and reprocessing materials inside the refinery.
Several examples of these recycling practices are listed below:
Recycling Activities
• Approximately 1.4 million barrels of oil is recovered from refinery process water each year and recycled back into our units to be converted to sale-able products.
• Process by-product gas is treated to remove 99.96 percent of its H2S and used as fuel gas, reducing natural gas purchases by approximately 39 billion standard cubic feet per year
• Approximately 174 billion gallons per year of cooling water is recirculated through the refinery
• Approximately 1.7 billion gallons per year of condensate recovered from the refinery steam system is reused as boiler feed water
• Approximately 470 million gallons per year of sour process water are treated to recover approximately 19,000 tons ammonia and 365,000 tons of sulfur. Both chemicals are sold to fertilizer manufacturers. Most of the water is re-used in refinery processes to remove salts
• Approximately 2,324 tons of spent catalyst are recycled each year through metallurgical smelters to recover the metals for reuse in the steel and copper industry
• Approximately 5,445 tons of scrap metal are recycled each year
• Approximately 55,860 barrels of oily solids material are recycled into the refinery processes and not sent off site as waste each year
• Approximately 97,930 tons of spent acid are sent from the refinery for recycling each year
• Approximately 199,005 pounds of paper products are recycled each year
• Approximately 2,688 yards of waste concrete are recycled each year
Chevron’s Environmental Management Company (EMC) has actively managed a corrective action program at the refinery since the 1990’s. Corrective action is a program designed to investigate and guide the cleanup of any contaminated groundwater or soil from spills or releases that have occurred in the refinery over years of operation.
In September 2009, the Pascagoula Refinery attained a significant environmental milestone. The refinery achieved the U.S. Environmental Protection Agency’s designation of “Corrective Action Remedy Construction Complete With Controls,” known as the CA550. This designation is the culmination of more than 32 years of work investigating and installing technically sound and innovative means of controlling and cleaning waste on refinery property. The refinery has spent approximately $100 million on corrective action work of this kind since 1998 and EMC continues to manage various remediation projects in the refinery today.In 2015, the U.S. Environmental Protection Agency (EPA) published a new rule requiring all petroleum refineries to conduct monitoring for benzene emissions along facility fencelines beginning in 2018. The program is intended to help refineries know where emissions or other problems may be occurring and is an addition to existing monitoring, leak detection routines, and environmental permits. In accordance with EPA guidance, the Refinery is conducting monitoring and reporting the results of that monitoring to the EPA. This data became available to the public through the EPA beginning June 14, 2019.
The Refinery collects air samples from 22 fixed locations around the property boundary. Chevron analyses the monitoring data to identify and address potential sources of benzene emissions. If that analysis indicates the Refinery exceeds the action level the Refinery performs the required root cause analysis, and takes steps to reduce and maintain emissions below the action level.
Protecting people and the environment is one of Chevron’s core values. We strive to operate safely and responsibly in all our locations. As long-time community partners in Jackson County, we are committed to continuing to improve this site’s environmental performance.
Air sampling and reporting to the EPA is a continuous process, and new data will continue to be collected, provided to and made available via the EPA’s website.
For more information about the EPA Petroleum Refinery Fenceline Monitoring rule, visit the EPA's reporting website.