conserving natural resources
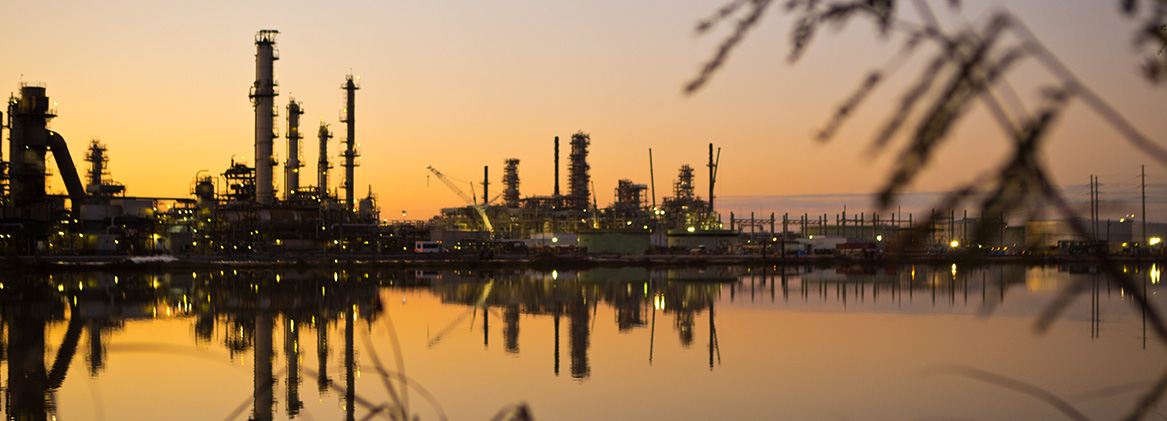
saving water
We use water to produce steam and to keep the Refinery product streams and equipment cool, similar to the cooling system in cars.
Cooling the water in large wooden “cooling towers” and re-circulating it minimizes the amount of fresh water needed. The water falls in droplets from the top to the bottom of the cooling tower. Large fans pull air from the bottom to the top.
The falling water cools when it encounters the rising air and forms billowing clouds of steam. These plumes of white clouds, which can be seen from miles away, are not smoke. Rather, they consist of condensed water vapor that is formed during the cooling process.
The clouds behave like fog, dissipate quickly, and do not harm the environment.
The Refinery’s water re-circulation rate for cooling systems is about 400 million gallons per day. Steam condensate recovery and recycle are about 7 million gallons per day.
water source
All the water used in the Refinery’s processes is supplied by the Jackson County Industrial Water System, which draws from the Pascagoula River and not from groundwater resources.
The water is pumped from the river through dual pipelines to the Bayou Casotte treating facility where clarification, filtration, and pH adjustments are done. Treated water is transported by pipeline to the Refinery and other Bayou Casotte area industrial users.
To replenish evaporative and consumed water losses, the Refinery uses about 16 million gallons of water per day from the Jackson County Industrial Water System, which is operated by the Jackson County Port Authority.
saving energy
The Refinery has a dedicated team of Energy specialists who work with all of our work groups to make continuous improvements in Energy Management. They work continuously to maintain Furnaces, Boilers, and Gas Turbines tuned to their optimum operating points for maximum energy efficiency. In addition, we use an optimizer built on linear programming principles to maintain our steam headers in good balance to prevent excessive letdowns or venting of steam.
Our Energy Team utilizes sophisticated real-time monitoring tools and software to determine when efficiency opportunities appear on any piece of equipment. So, in addition to monitoring the overall Refinery efficiency, we evaluate the efficiencies of individual turbines, compressors, pumps, power recovery turbines, etc. This same level of scrutiny is also applied to our utility streams – nitrogen, compressed air, electricity, lube oils, cooling water, condensate, etc. – to ensure that we don’t waste these valuable resources.
Finally, our Refinery is continually evaluating and applying new technologies to save even more energy. For example, about nine years ago, we converted our standard insulation to a new space-age insulation that has a better thermal resistance which can save more energy. And, more recently, we have been on a program of installing LED lighting in the exterior plant lighting systems as well as inside of our office buildings, warehouses, and Control Rooms.
vapor recovery
loading displaces vapors
During loading of bulk liquid tankers or barges, the liquid introduced displaces vapors from previous cargoes that still exist in the tank and those vapors generated by the current cargo loading. The vapors of certain cargoes contain volatile organic compounds (VOCs) that include hydrocarbons, oxygenated hydrocarbons, and organic compounds containing nitrogen or sulfur.
chevron marine vapor recovery system meets federal requirements
Our Title V Operating Permit requires the control of VOC emissions, and the Marine Vapor Recovery units at the refinery’s marine facility meet Coast Guard and Clean Air Act requirements. The Pascagoula Refinery’s Marine Vapor Recovery system includes two units.
marketing terminal vapor recovery unit
As a tank truck drops (delivers) new product into the underground storage tank at Chevron gas stations, the vapors created during the drop are pushed back into the tank truck and stored there.
As the tank truck loads new product at the Marketing Terminal using a “bottom loading” method, the product being loaded into the bottom of the tank pushes the collected vapors into a vapor recovery hose connected to the recovery system. The Adsorb/Absorb vapor recovery unit condenses the vapors, recovering about 2 gallons of gasoline per 1000 gallons loaded product.